LDD records and communicates real-time data for every part before, during, and after each weld. In the event of process degradation or
weld failures, LDD alerts operators and systems to take corrective action. This intelligent process monitoring ensures that normal operations can
resume quickly and that only good parts move on in your manufacturing pipeline.
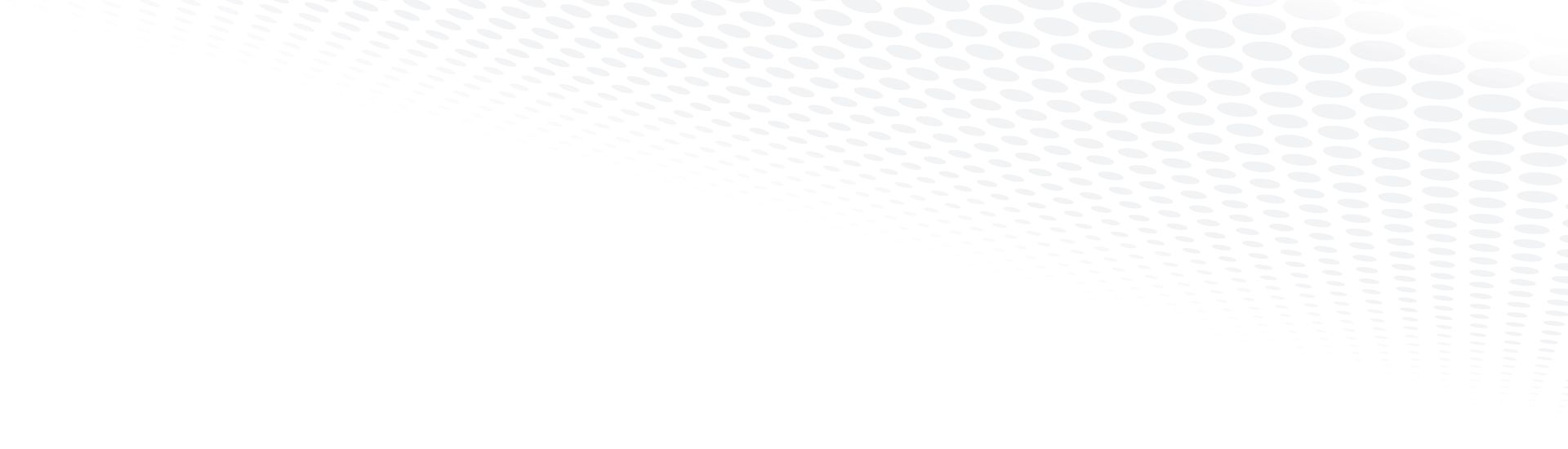
LDD Real-Time Laser Weld Measurement
Inline Weld Process Monitoring
Direct Weld Measurement
100% Quality Assurance
Real-Time Monitoring
Utilizing a low-power beam fired through the same optics as the welding laser, LDD measures every weld as it is made for highly accurate 100% quality assurance.
Direct, geometric measurement of weld penetration and 20+ other weld characteristics provides instant data comparable to destructive cross-sectioning without destroying the part.
Direct Weld Measurement
100% Quality Assurance
Real-Time Monitoring
Utilizing a low-power beam fired through the same optics as the welding laser, LDD measures every weld as it is made for highly accurate 100% quality assurance.
Direct, geometric measurement of weld penetration and 20+ other weld characteristics provides instant data comparable to destructive cross-sectioning without destroying the part.
Get the Most Out of Laser Welding
100% In-Process Weld Inspection

Weld Depth
Direct weld depth measurement ensures under- or over-penetration does not compromise joint strength or electrical performance.

Seam Position
Scanning ahead of the weld to confirm part alignment and weld path enables automatic seam realignment if necessary.

Transverse Profile
Measuring the weld seam's bead width and shape detects overfill, underfill, or edge undercut that can indicate a weak finished joint.

Finished Surface
Analyzing the finished weld surface checks for defects that may indicate reduced structural integrity or increased electrical resistance.

Weld Verification — The IPG Difference
Unlike most weld monitoring techniques that simply monitor imperfect weld quality indicators like weld plume, LDD performs direct weld penetration measurements and 3D imaging to see exactly what the welding beam sees.
Compared to alternative technologies, LDD provides:
- Full penetration weld depth measurement & quality assurance
- Compatibility with single-mode laser welding
- 3D imaging of keyhole and live 3D viewing for robot teaching
- Keyhole alignment in any direction
- Compatibility with high-speed on-the-fly welding
Direct Weld Measurement Increases ROI
technologies like photodiode monitoring rely on indrect weld measurements like weld plume height that often lead to a high rate of false failures.

Smarter Laser Welding


Seamless Integration with IPG Lasers & Beam Delivery
LDD integrates effortlessly with IPG fiber lasers, process heads, and welding systems. IPG OmniWELD software steers the measurement beam to measure key weld dimensions with no interruption to the welding process.
The optimal combination of measurement parameters and pass/fail criteria for each weld process is easily configured and replicated across systems.
LDD-700 Specifications
![]() |
LDD-700 |
Real-Time Weld Measurement |
LDD-700 |
Real-Time Weld Measurement |
Measurement Technology |
---|
Inline Coherent Imaging |
Weld Measurements |
20+ Weld Metrics |
Imaging Wavelength |
800 to 900 nm |
Power |
<20 mW |
Measurement Frequency |
250 kHz |
Head Interface Compatibility |
Virtually All Fixed-Optic Camera Ports |
Cooling |
Air-Cooled |
Learn More |
|
||||
|
||||
Measurement Technology | Inline Coherent Imaging | |||
Weld Measurements | 20+ Weld Metrics | |||
Imaging Wavelength | 800 to 900 nm | |||
Power | <20 mW | |||
Measurement Frequency | 250 kHz | |||
Head Interface Compatibility | Virtually All Fixed-Optic Camera Ports | |||
Cooling | Air-Cooled | |||
Learn More |
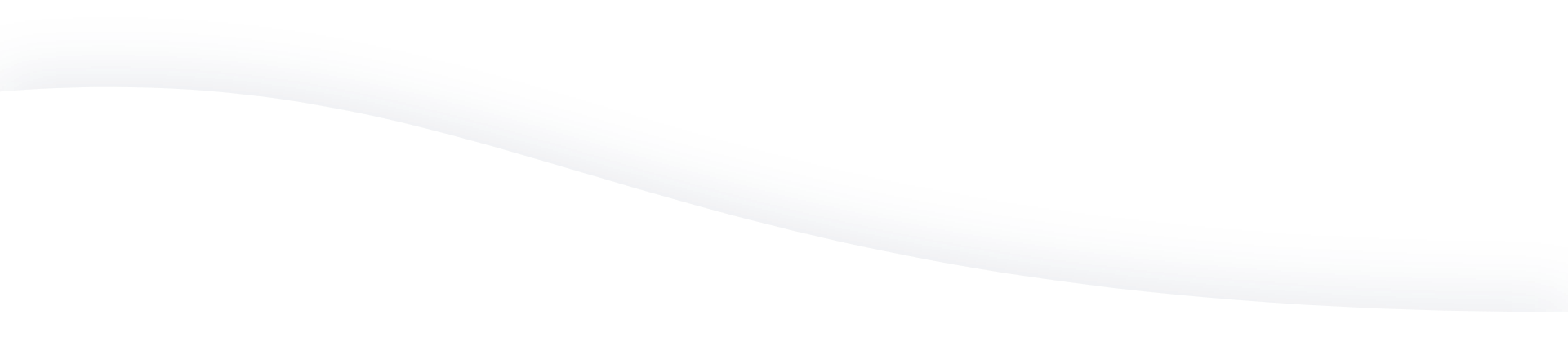