About the Company
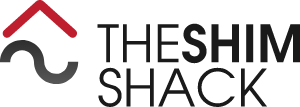
The Shim Shack is a family-owned and operated sheet metal fabrication shop. Founded in 1974 by two brothers in a two-car garage, the shop has since grown to more than 160 employees. The company serves a wide range of customers including NASA, Tesla, and Boston Dynamics.
Challenges
Achieving quick turnaround: The Shim Shack has established themselves as a shop that can meet last-minute customer demands, often delivering parts within a day or two. The company must be able to receive customer requirements and turn them around with a high level of quality quickly, even when customers required high volumes of smaller parts.
Projects sometimes took the shop weeks or months from start to finish, forcing the company to rely on keeping parts ready on the shelf.
Cutting a variety of thin metals: as the name would suggest, The Shim Shack primarily manufacturers and delivers shims and other small, thin parts. Cutting material as thin as .001" on the company's larger machines was a recurring challenge.
The Solution

The Shim Shack had looked for years for a machine with a smaller footprint that could handle smaller parts. Some employees had worked with CO2 lasers in the past but were more interested in fiber laser technology.
Management at the company searched for a fiber laser cutting solution before discovering and choosing the IPG LaserCube Flatbed Laser Cutting System. The system is purpose-built for cutting metal sheets from thin foils to 3/4" thick steels. The machine easily handles the materials The Shim Shack frequently cuts, including steels, stainless steels, aluminum, copper, and brass.
The LaserCube system combines a reliable, energy efficient, and compact IPG fiber laser with high-speed, high-accuracy system motion. The machine can cut hundreds of small parts per hour, enabling the company to transform their turnaround from weeks to days. This leap in productivity helps support The Shim Shack's focus on custom requests and their website, which allows customers to design and order custom shims. Customer designs are automatically sent to the sales team who then convert them into design files and cutting paths for the LaserCube system. The ability to deliver on these custom projects helps the shop stay competitive and look attractive to current and prospective customers.
Laser cutting and the LaserCube system proved to be such a good solution for The Shim Shack that they ultimately installed multiple machines. The shop also reworked some of their processes to put more focus on the LaserCube and its capabilities. The laser cutting success also prompted the company to introduce IPG laser marking technology to the production floor. This capability gives The Shim Shack the opportunity to increase their capabilities and produce new products and features.
Working with IPG
IPG is more than just a laser company — we are a global laser solutions provider and single vendor source for everything from industry-leading laser technology to custom laser systems. At IPG we combine laser expertise with industry know-how to offer solutions that maximize the power of laser processing, minimize risk, and enable sustainable manufacturing.
Are you considering a laser processing solution? Getting started is easy — send us a sample, visit one of our global application labs, or just tell us about your application.
Get Started