Over het bedrijf
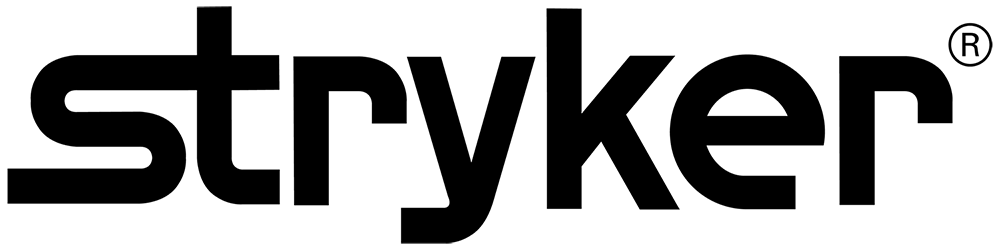
Stryker begon bescheiden toen Dr. Homer Stryker, een orthopedisch chirurg die ontevreden was over de beschikbare medische hulpmiddelen, in 1941 Wedge Turning Frames begon te produceren. Dit innovatieve product gaf prioriteit aan het comfort van de patiënt, zodat zorgverleners patiënten met ernstig rugletsel konden draaien terwijl de wervelkolom geïmmobiliseerd bleef.
Vandaag de dag is Stryker een wereldleider in medische technologie en een Fortune 500-bedrijf. Met ongeveer 52.000 werknemers wereldwijd en $1,4B uitgegeven in R&D in 2023, zet Stryker zijn traditie van innovatie voort met een focus op het leveren van producten en diensten die de resultaten van patiënten en de gezondheidszorg verbeteren.
De uitdaging
Bij de ontwikkeling van de volgende generatie instrumenten voor sinusdilatatie met een ballon (BSD) stond een van de productontwerp- en engineeringteams van Stryker voor de uitdaging om de kosten te verlagen en de opbrengst te verbeteren. BSD is een veilige en eenvoudige procedure die wordt gebruikt bij de behandeling van chronische rhinosinusitis, een aandoening waaraan één op de acht Amerikanen lijdt. Door de kosten van BSD-apparaten te verlagen, zou Stryker meer artsen van apparatuur kunnen voorzien, waardoor meer patiënten van de procedure zouden kunnen profiteren.
Terwijl er werd nagedacht over manieren om de productie-efficiëntie te verbeteren door het ontwerp aan te passen, was het behoud van de kwaliteit van een gelaste subassemblage van cruciaal belang. Falen van dit ontwerpelement kon gevolgen hebben voor andere aspecten van het ontwerp en mogelijk de voortgang van het project verstoren. Ontwerpers en ingenieurs waren ook niet bereid om concessies te doen aan de prestaties of kwaliteit van het eindproduct.
Om de uitdaging nog groter te maken, was interne ontwikkeling geen optie, omdat de productiefaciliteit van Stryker op volle productiecapaciteit draaide.
Het bedrijf, dat al verschillende IPG-precisielaserlassystemen gebruikte, wilde er zeker van zijn dat eventuele wijzigingen in het productieproces compatibel zouden zijn met hun huidige IPG-systemen. Dit zou een naadloze overgang van R&D naar volledige productie mogelijk maken wanneer het bijgewerkte product zou worden goedgekeurd.
De oplossing
Design Engineer Vinunti Trivedi benaderde IPG voor een oplossing en gaf de laserexperts van IPG de opdracht een nieuw precisielasproces te ontwikkelen. Volgens Trivedi "was de beste optie om IPG te bellen om te onderzoeken wat de beste aanpak was om de las uit te voeren. IPG weet hoe ze hun technologie veel sneller kunnen optimaliseren dan we zelf zouden kunnen."
Omdat bij de projectbesprekingen verschillende Stryker-teams in Ierland en de VS betrokken waren, was effectieve communicatie essentieel om ervoor te zorgen dat aan de hoge eisen van het project werd voldaan. Door met IPG samen te werken aan de ontwikkeling van een nieuw lasproces parallel aan andere facetten van de productupdate, kon het bedrijf de risico's van de lasstap elimineren en zich richten op andere aspecten van het ontwerp.
Uiteindelijk ontwikkelde IPG met succes een lasproces dat voldeed aan de behoeften van Stryker en dat de levensduur van hun huidige systeem verlengde tot de volgende generatie producten.
Werken met IPG
IPG is meer dan alleen een laserbedrijf - we zijn een wereldwijde leverancier van laseroplossingen en één leverancier voor alles van toonaangevende lasertechnologie tot lasersystemen op maat. Bij IPG combineren we laserexpertise met kennis van de industrie om oplossingen te bieden die de kracht van laserbewerking maximaliseren, risico's minimaliseren en duurzame productie mogelijk maken.
Overweegt u een laserbewerkingsoplossing? Aan de slag gaan is eenvoudig - stuur ons een monster, bezoek een van onze wereldwijde applicatie laboratoria, of vertel ons gewoon over uw applicatie.
Aan de slag