About the Company
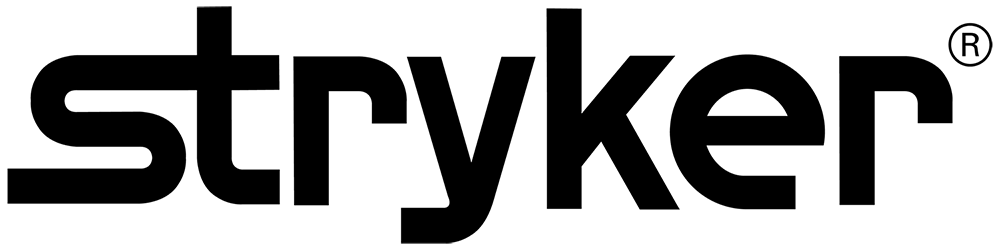
Stryker started from humble beginnings when Dr. Homer Stryker, an orthopedic surgeon dissatisfied with the available medical tools, began producing Wedge Turning Frames in 1941. This innovative product prioritized patient comfort, allowing caregivers to turn patients with serious back injuries while keeping the spine immobilized.
Today Stryker is a world leader in medical technology and a Fortune 500 company. With about 52,000 employees worldwide and $1.4B spent in R&D in 2023, Stryker continues their tradition of innovation with a focus on providing products and services that improve patient and healthcare outcomes.
The Challenge
When developing the next generation of balloon sinus dilation (BSD) tools, one of Stryker’s product design and engineering teams was challenged to reduce costs and improve yields. BSD is a safe and easy procedure used in the treatment of chronic rhinosinusitis, a condition affecting one in eight Americans. Reducing the costs of BSD tools would enable Stryker to provide equipment to more physicians, allowing more patients to benefit from the procedure.
While considering ways to improve manufacturing efficiency via design alteration, maintaining the quality of a welded subassembly was critically important. Failure of this design element could impact other aspects of the design and potentially disrupt the project’s progress. Designers and engineers were also not willing to compromise on the performance or quality of the final product.
To add to the challenge, internal development was not an option, as the Stryker manufacturing facility was running at full production capacity.
The company, who was already utilizing several IPG precision laser welding systems, wanted to ensure that any changes to the manufacturing process would be compatible with their current IPG systems. This would allow for a seamless transition from R&D to full production when the updated product was approved.
The Solution
Design Engineer Vinunti Trivedi reached out to IPG for a solution, tasking IPG laser experts with developing a new precision welding process. According to Trivedi, “The best option was to call IPG to investigate the best approach to perform the weld. IPG knows how to optimize their technology much faster than we could do in house.”
With project discussions involving several Stryker teams located in Ireland and the US, effective communications were essential to ensure the demanding requirements of the project were met. By working with IPG to develop a new welding process in parallel with other facets of the product update, the company was able to eliminate risk associated with the welding step and focus their efforts on other aspects of the design.
Ultimately, IPG successfully developed a welding process that met Stryker’s needs and extended the service life of their current system to the next generation of products.
Working with IPG
IPG is more than just a laser company – we are a global laser solutions provider and single vendor source for everything from industry-leading laser technology to custom laser systems. At IPG we combine laser expertise with industry know-how to offer solutions that maximize the power of laser processing, minimize risk, and enable sustainable manufacturing.
Are you considering a laser processing solution? Getting started is easy – send us a sample, visit one of our global application labs, or just tell us about your application.
Get Started