- Home
- Real-Time Weld Measurement

Real-Time Weld Measurement
ENSURE
MINIMIZE
Cost-Per-Part
Decrease scrap and rework and eliminate time-consuming and destructive weld testing.
MAXIMIZE
Traceability
Track and record critical key weld metrics and integrate with manufacturing systems.
What is Real-Time Laser Weld Measurement?
Real-time laser weld measurement directly measures 20+ weld metrics before, during, and after the welding process. This innovative solution provides unmatched in-process Quality Assurance (QA) to enable manufacturers to weld faster, more cost-effectively, and with unmatched confidence.
Despite the stability and repeatability of laser welding, unexpected material properties can result in imperfect welds. Traditional weld QA often involves time consuming post process steps like resistance testing or destructive cross sectioning that provide incomplete data.
Direct Measurement of Key Weld Metrics

Weld Depth
Direct weld depth measurement ensures under- or over-penetration does not compromise joint strength or electrical performance.

Seam Position
Scanning ahead of the weld to confirm part alignment and weld path enables automatic seam realignment if necessary.

Transverse Profile
Measuring the weld seam's bead width and shape detects overfill, underfill, or edge undercut that can indicate a weak finished joint.

Finished Surface
Analyzing the finished weld surface checks for defects that may indicate reduced structural integrity or increased electrical resistance.
Photodiode Measurement vs. Real-Time Measurement
Alternative in-process laser weld measurement technologies like photodiode rely on indirect measurement of weld quality indicators like weld plume, back reflection, and heat-affected zone. These imprecise process characteristics provide unreliable correlations with weld quality and must be calibrated on a per-process basis. Since pass/fail parameters are based on indirect data, confidence in final part quality requires unnecessarily aggressive failure conditions that result in a high rate of false failure and part scrap or rework.
By comparison, LDD real-time weld measurement provides direct, distance-based measurements of critical geometries like weld depth. LDD technology does not rely on in-process indicators and offers direct monitoring of pre-weld, in-weld, and post-weld measurements in parallel. Micron-scale precision on direct weld quality measurements enables significantly tighter QA tolerances that dramatically reduce false failures.
Technology
Measurement & Validation
Measurement Accuracy
False Failures
Process Flexibility
Photodiode Weld Monitoring
TechnologyPhotodiode Sensors
Measurement & ValidationIndirect Measurement
Measurement AccuracyModerate
False FailuresHigh
Process FlexibilityRequires Process-Specific Calibration
LDD Real-Time Weld Measurement
TechnologyInterferometric Ranging
Measurement & ValidationDirect, Geometric Measurement
Measurement AccuracyHigh
False FailuresVirtually None
Process FlexibilityNo Calibration Required

Weld Verification — The IPG Difference
Unlike most weld monitoring techniques that simply monitor imperfect weld quality indicators like weld plume, LDD performs direct weld penetration measurements and 3D imaging to see exactly what the welding beam sees.
Compared to alternative technologies, LDD provides:
- Full penetration weld depth measurement & quality assurance
- Compatibility with single-mode laser welding
- 3D imaging of keyhole and live 3D viewing for robot teaching
- Keyhole alignment in any direction
- Compatibility with high-speed on-the-fly welding

Laser Weld Measurement for Industry 4.0 Webinar
In this on-demand webinar, learn how direct in-process weld measurement can help you reduce scrap and identify defects earlier to save time and reduce operating costs.
Watch Now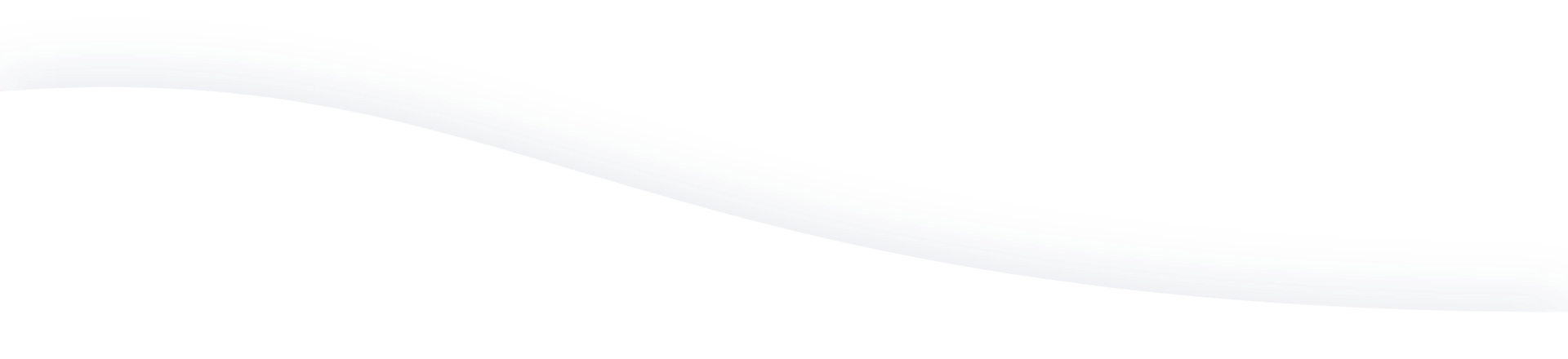