- 홈
- LDD 레이저 용접 모니터링

LDD 레이저 용접 모니터링
ENSURE
부품당 비용 최소화
불량품과 재작업을 줄이고 시간이 많이 걸리고 파괴적인 용접 테스트를 없앨 수 있습니다.
추적성 극대화
중요한 주요 용접 메트릭을 추적 및 기록하고 제조 시스템과 통합합니다.
실시간 레이저 용접 측정이란 무엇인가요?
실시간 레이저 용접 측정은 용접 프로세스 전, 도중, 후에 20개 이상의 용접 메트릭을 직접 측정합니다. 이 혁신적인 솔루션은 타의 추종을 불허하는 공정 중 품질 보장(QA)을 제공하여 제조업체가 더 빠르고 비용 효율적이며 자신 있게 용접할 수 있도록 지원합니다.
레이저 용접의 안정성과 반복성에도 불구하고 예상치 못한 재료 특성으로 인해 불완전한 용접이 발생할 수 있습니다. 기존의 용접 QA에는 종종 불완전한 데이터를 제공하는 저항 테스트 또는 파괴적 단면 분석과 같은 시간이 많이 소요되는 후처리 단계가 포함됩니다.
주요 용접 메트릭의 직접 측정

용접 깊이
(Weld Depth)
직접 용접 깊이를 측정하여 과소 또는 과잉 침투로 인해 조인트 강도나 전기 성능이 저하되지 않도록 보장합니다.

심 포지션
(Seam Position)
용접 전 스캔을 통해 부품 정렬과 용접 경로를 확인하여 필요한 경우 자동으로 이음새를 다시 정렬할 수 있습니다.

비드의 너비
(Transverse Profile)
용접부의 비드 폭과 모양을 측정하여, 오버필, 언더필 또는 가장자리 언더컷이 발생했는지를 감지하고 이를 통해 용접 강도 저하를 방지합니다.

비드의 높이
(Finished Surface)
용접부 표면을 분석하여 구조적인 용접 특성 감소 또는 전기 저항 증가를 초래하는 결함이 있는지 확인합니다.
광 다이오드 측정 대 실시간 측정
포토다이오드를 활용한 용접 측정 기술은 발생한 용접 plume, 반사빔, 열 영향과 같은 용접 품질 지표에 의존한 "간접적인 측정"입니다. 이러한 지표는 공정품질에 대하여 상관 관계를 추정할 수 있는 정보만을 제공하기때문에 신뢰하기 어렵고, 더 나아가 공정별로 매번 품질기준을 보정해야 하는 문제가 있습니다. 또한 합격/불합격 파라미터는 간접 데이터를 기반으로 하기 때문에 최종 부품 품질에 대한 신뢰도를 높이려면 불필요하게 넓은 범위의 불량 조건 설정을 하게되며, 이는 높은 불합격율과 부품 스크랩 또는 재작업으로 이어집니다.
이에 비해 LDD 실시간 용접 측정은 용접 깊이와 같은 중요한 형상을 거리 기반으로 하는 "직접적인 측정방식"입니다. LDD 기술은 공정 중 발생하는 간접적인 다른 지표에 의존하지 않으며, 거리 측정 기반으로 용접 전, 용접 중, 용접 후 측정을 동시에 직접 모니터링할 수 있습니다. 직접 용접 품질 측정에 대한 미크론 단위의 정밀도를 통해 훨씬 더 엄격한 QA 허용 오차를 구현하여 잘못된 실패를 획기적으로 줄일 수 있습니다.
기술
측정 및 검증
측정 정확도
거짓 실패
프로세스 유연성
광 다이오드 용접 모니터링
포토다이오드센서
간접측정
측정 정확도보통
거짓 실패 높음
프로세스 유연성프로세스별캘리브레이션 필요
LDD 실시간 용접 측정
간섭 거리 측정
직접적이고 기하학적인 측정
측정 정확도 높음
허위 실패 거의없음
프로세스 유연성보정필요 없음

용접 검증 - IPG의 차별점
용접 플룸(Plume)과 같은 불완전한 용접 품질 지표를 단순히 모니터링하는 그 상관관계를 제공하는 대부분의 용접 모니터링 기술과 달리, LDD 측정빔는 용접시 키홀을 직접 관통 측정하고 3D 이미징을 수행하여 용접 빔과의 위치 동기화를 통해 정확한 용접 품질을 측정 합니다.
대체 기술과 비교했을 때 LDD는 다음과 같은 이점을 제공합니다:
- 전체 관통 용접 깊이 측정 및 품질 보장
- 싱글 모드 레이저 용접과의 호환성
- 로봇 교육을 위한 키홀의 3D 이미징 및 실시간 3D 보기
- 모든 방향으로의 키홀 정렬
- 고속 온더플라이 용접과의 호환성

4차 산업혁명을 위한 레이저 용접 측정
웨비나에서 공정 중 용접을 직접 측정하여 불량품을 줄이고 결함을 조기에 식별하여 시간을 절약하고 운영 비용을 절감하는 방법을 알아보세요.
지금 보기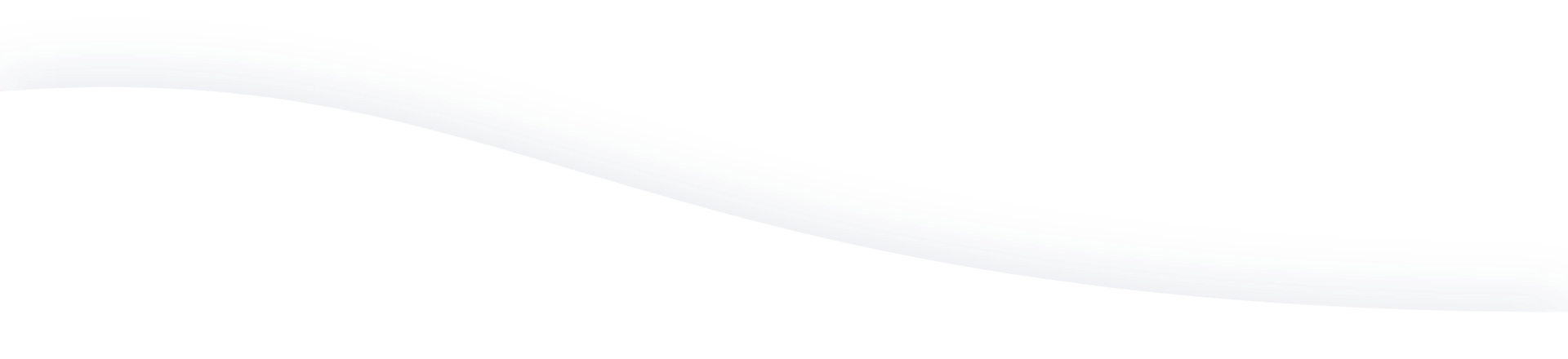